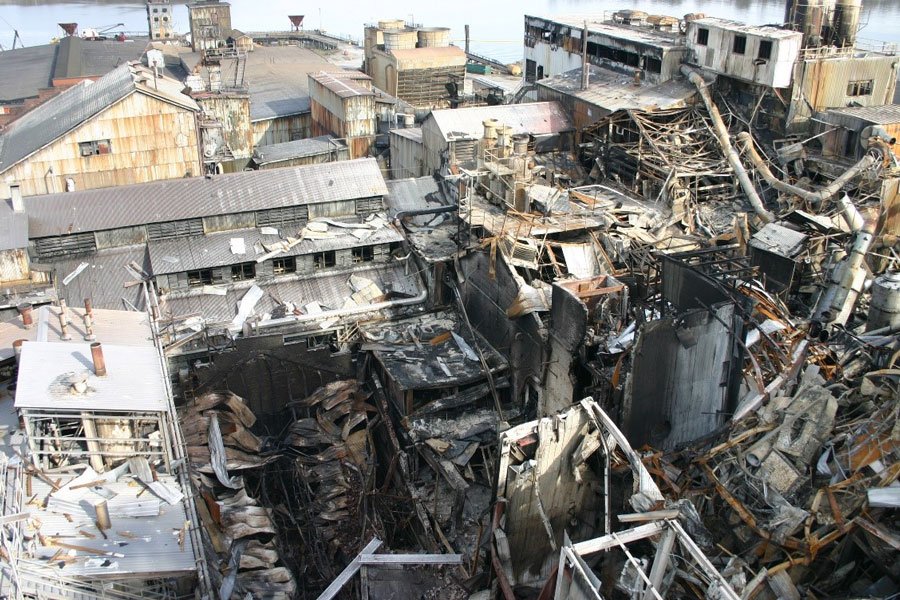
Watching the sparks fly to guard against disaster
Handling dusty materials in industrial processes is a tricky business, raising numerous safety and housekeeping concerns that need to be handled by plant managers. One aspect of dusts that can easily be overlooked goes far beyond being a mere nuisance – it could jeopardise the existence of your factory and the lives of your workers. It’s the threat of dust explosions.
Many common materials react with the oxygen in air, which is the basis of combustion. Some, such as iron and aluminium, form a layer of oxide on their surfaces at ambient temperatures. Pieces of natural fibres such as wood or cotton will burn if heated strongly, but only fairly slowly. However, materials that can react with oxygen will do so increasingly quickly as they become more and more finely divided, because the surface area of the material that is exposed to the air sharply increases.
In most cases, this effect reaches its climax when the material exists as a fine dust dispersed in a stream of air within a confined space such as a vessel or duct. At this point, a relatively weak ignition source such as a spark can, under the right conditions, cause the material to burn extremely rapidly. This releases heat to the surrounding gases in the air, which then expand and cause an enormous increase in pressure – and a dust explosion occurs.
The image shows the aftermath of a sugar dust explosion and the resulting fire
Dust explosions can be highly destructive and often occur completely without warning. They can almost instantly increase the pressure inside a chamber by eight or nine times normal atmospheric pressure, far exceeding the resistance of most vessels. In addition to the shockwave from the explosion, operators are then at risk from fire and the shrapnel from fragmented vessel walls. Furthermore, the explosion fireball can travel along interconnecting pipes and cause an even more violent explosion in another vessel downstream.
Image source: US Chemical Safety and Hazard Investigation Board